Introduction to Concrete Foaming Agents: Allowing the Rise of Lightweight, Energy-Efficient Concrete Systems
Concrete foaming agents have actually emerged as a transformative component in modern building, allowing the manufacturing of light-weight oxygenated concrete with enhanced thermal insulation, lowered structural tons, and enhanced workability. These specialized surfactants produce stable air bubbles within the concrete matrix, causing products that combine toughness with low density. As urbanization increases and sustainability comes to be a core priority in structure layout, lathered concrete is gaining traction throughout household, commercial, and facilities tasks for its convenience and ecological benefits.
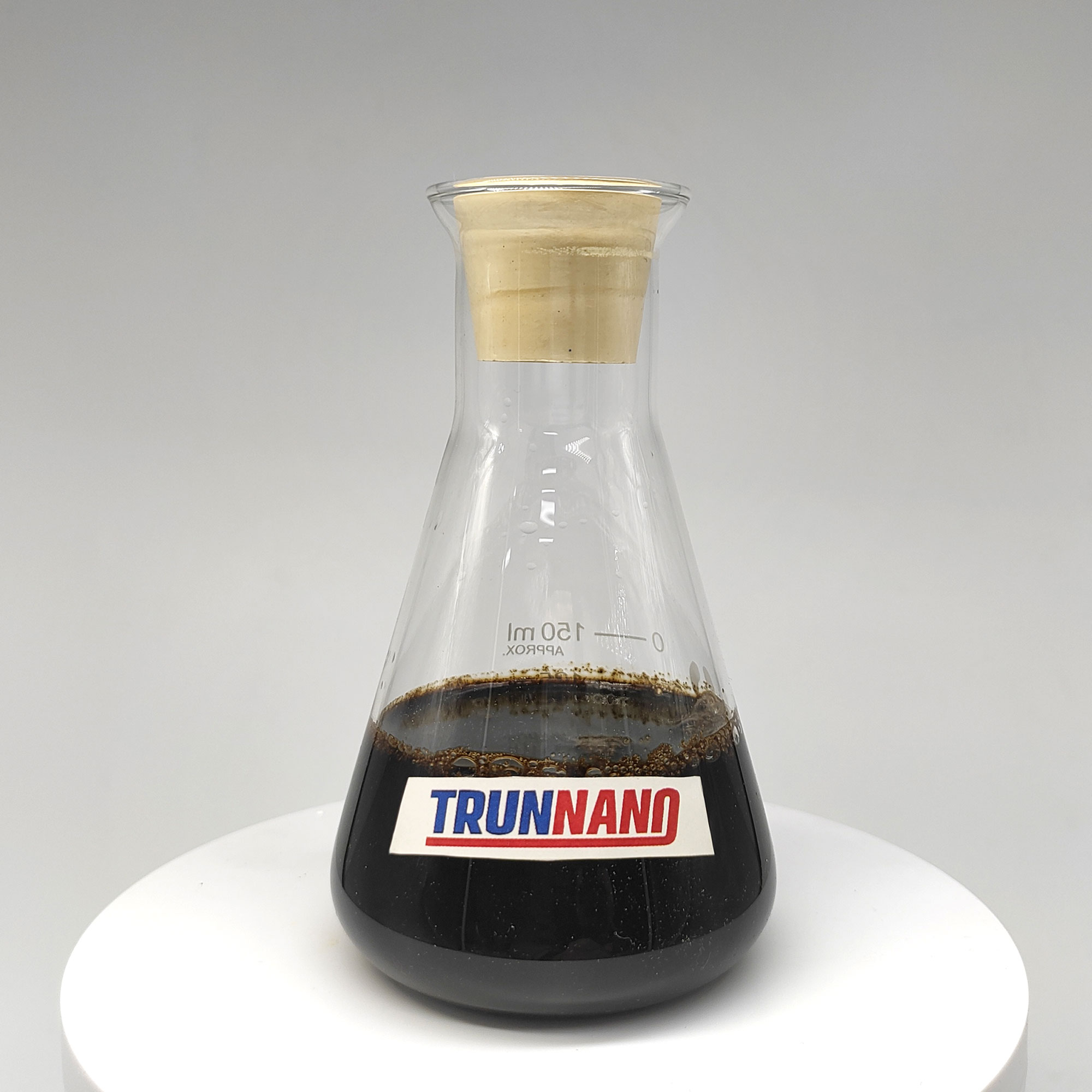
(Concrete foaming agent)
Chemical Structure and System of Action
Concrete frothing representatives are usually based on protein hydrolysates, artificial surfactants, or crossbreed solutions designed to maintain air bubbles throughout blending and healing. When presented into the concrete slurry, these representatives lower surface stress and facilitate the development of uniform, fine-cell foam structures. The security of the foam is important– poorly stabilized bubbles can integrate or collapse, leading to irregular density and jeopardized mechanical residential or commercial properties. Advanced lathering agents now include nano-additives and rheology modifiers to boost bubble retention, flowability, and early-age toughness development in foamed concrete systems.
Manufacturing Refine and Foam Stability Considerations
The production of foamed concrete includes 2 main methods: pre-foaming and blended foaming. In pre-foaming, air is created independently utilizing a foaming equipment prior to being combined right into the cementitious combination. Combined foaming presents the foaming representative directly into the mixer, generating bubbles sitting. Both methods call for accurate control over foam generation, dosage prices, and mixing time to guarantee optimal efficiency. Aspects such as water-to-cement proportion, ambient temperature, and concrete reactivity dramatically influence foam stability, prompting recurring research into adaptive frothing systems that preserve consistency under varying conditions.
Mechanical and Thermal Properties of Foamed Concrete
Foamed concrete exhibits a distinct combination of mechanical and thermal attributes that make it ideal for applications where weight decrease and insulation are critical. Its compressive strength varieties from 0.5 MPa to over 10 MPa depending on density (typically in between 300 kg/m ³ and 1600 kg/m six). The existence of entrapped air cells dramatically improves thermal insulation, with thermal conductivity worths as reduced as 0.08 W/m · K, measuring up to conventional insulating materials like broadened polystyrene. Additionally, frothed concrete deals fire resistance, acoustic damping, and wetness regulation, making it ideal for both architectural and non-structural components in energy-efficient structures.
Applications Throughout Residential, Commercial, and Facilities Sectors
Frothed concrete has actually discovered prevalent use in flooring screeds, roofing system insulation, gap filling, and premade panels due to its self-leveling nature and simplicity of positioning. In domestic building, it acts as an effective thermal barrier in wall surfaces and foundations, contributing to easy energy savings. Industrial developers utilize foamed concrete for raised gain access to floorings and shielded partitions. Facilities applications consist of trench backfilling, train trackbeds, and bridge abutments, where its low weight reduces earth stress and negotiation dangers. With expanding focus on eco-friendly building accreditations, frothed concrete is increasingly considered as a lasting option to standard thick concrete.
Ecological Advantages and Life Process Assessment
Among the most engaging benefits of foamed concrete depend on its reduced carbon footprint contrasted to traditional concrete. Lower product usage, decreased transportation costs as a result of lighter weight, and improved insulation efficiency all contribute to reduce lifecycle discharges. Many lathering representatives are originated from renewable or naturally degradable resources, even more supporting environment-friendly construction techniques. Studies have actually shown that replacing typical concrete with lathered choices in non-load-bearing applications can cut embodied carbon by as much as 40%. As governing structures tighten around discharges and resource effectiveness, frothed concrete sticks out as an essential enabler of lasting urban development.
Difficulties and Limitations in Practical Release

( Concrete foaming agent)
In spite of its lots of advantages, lathered concrete faces numerous obstacles that limit its fostering in conventional building. Concerns such as drying shrinkage, delayed setting times, and level of sensitivity to inappropriate blending can endanger efficiency otherwise carefully handled. Surface completing might also be more complex as a result of the permeable framework, requiring specialized finishings or toppings. From a supply chain viewpoint, schedule and price of high-performance lathering representatives stay barriers in some areas. Furthermore, long-lasting resilience under extreme weather conditions is still being evaluated with field tests and accelerated aging tests. Attending to these limitations calls for proceeded technology in formulation chemistry and construction approach.
Developments and Future Directions in Foaming Representative Growth
Research is proactively progressing towards next-generation frothing agents that offer exceptional efficiency, wider compatibility, and boosted ecological qualifications. Growths include bio-based surfactants, enzyme-modified healthy proteins, and nanotechnology-enhanced foams that improve mechanical stamina without giving up insulation homes. Smart foaming systems efficient in adapting to real-time mixing problems are being checked out, in addition to combination right into digital building and construction systems for automated dosing and quality assurance. As additive manufacturing push on in building, lathered concrete formulas suitable with 3D printing are also emerging, opening up new frontiers for building creative thinking and practical layout.
Distributor
Cabr-Concrete is a supplier under TRUNNANO of Concrete Admixture with over 12 years of experience in nano-building energy conservation and nanotechnology development. It accepts payment via Credit Card, T/T, West Union and Paypal. TRUNNANO will ship the goods to customers overseas through FedEx, DHL, by air, or by sea. If you are looking for Concrete foaming agent, please feel free to contact us and send an inquiry. (sales@cabr-concrete.com)
Tags: concrete foaming agent,concrete foaming agent price,foaming agent for concrete
All articles and pictures are from the Internet. If there are any copyright issues, please contact us in time to delete.
Inquiry us
Error: Contact form not found.